Micronclean ISO Class 6, Class 4 and PPE Service Offering
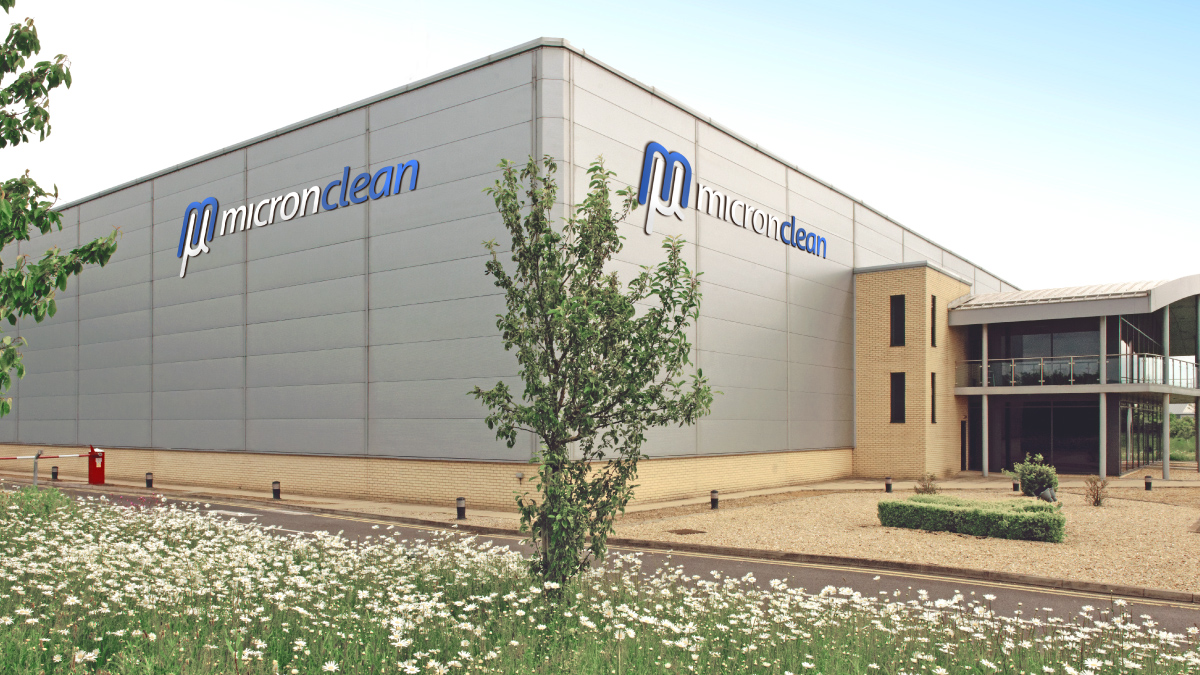
Our core service laundry facilities around Lincolnshire form the historical heart of our business via our three main sites.
ISO CLASS 6 LAUNDRY
In Louth, Micronclean operates one of the most technically advanced ISO Class 6 (GMP Grade C) Cleanroom Laundries in Europe, with the capacity to process in excess of 120,000 items a week. The Louth plant is highly automated and was purpose-built to exploit the power within our Protrack garment tracking system. Using Micronclean’s approved wash programs, garments are decontaminated using barrier washing machines before being transferred into our ISO Class 6 cleanroom, where they are individually bagged before being transferred to the warehouse prior to automatic final sorting and dispatch to the customer.
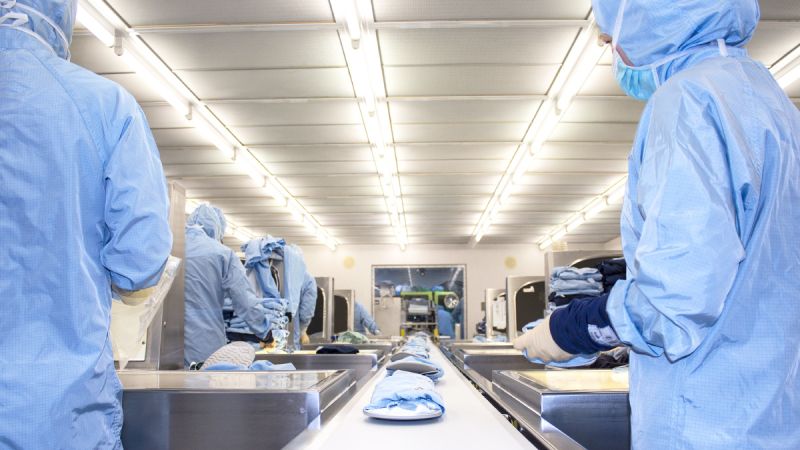
ISO CLASS 4 LAUNDRY
In Skegness, Micronclean operates the largest dedicated ISO Class 4 (GMP Grade B) Cleanroom Laundry in the UK which has a capacity of more than 70,000 garments a week. Using Micronclean’s validated cleanroom wash programs, items are decontaminated using barrier washing machines before transferring into our ISO Class 4 cleanroom. Cleanroom items are then placed into positive pressure, HEPA filtered air tumble dryers to complete the process and aid final particulate removal. The cleanroom items are then packaged and prepared for sterilisation (if required) before batch information for full traceability is added.
WORKWEAR BARRIER LAUNDRY
In addition to our Class 4 and Class 6 offerings, the laundry at Grantham has been developed over the years to become a dedicated PPE processing plant and is capable of processing over 40,000 garments a week. By using Micronclean's validated wash programs, which include appropriate levels of detergent, water and heat, to ensure that all the garments are clean before being unloaded into the clean area. Garments are hung on coat hangers and placed onto a rail system which conveys the garment to a 'Tunnel Finisher' dryer, then the quality inspection area where items needing rework are redirected to repairs, and items that are fit for the customers purpose are sent to semi-automatic folding machines and packed to the customer requirements ready for de. All the garment journeys throughout the plant are scanned at each stage through our Protrack system for full accountability.