Big Blue Blog - Cleanroom Cleaning - General Considerations - Part Two
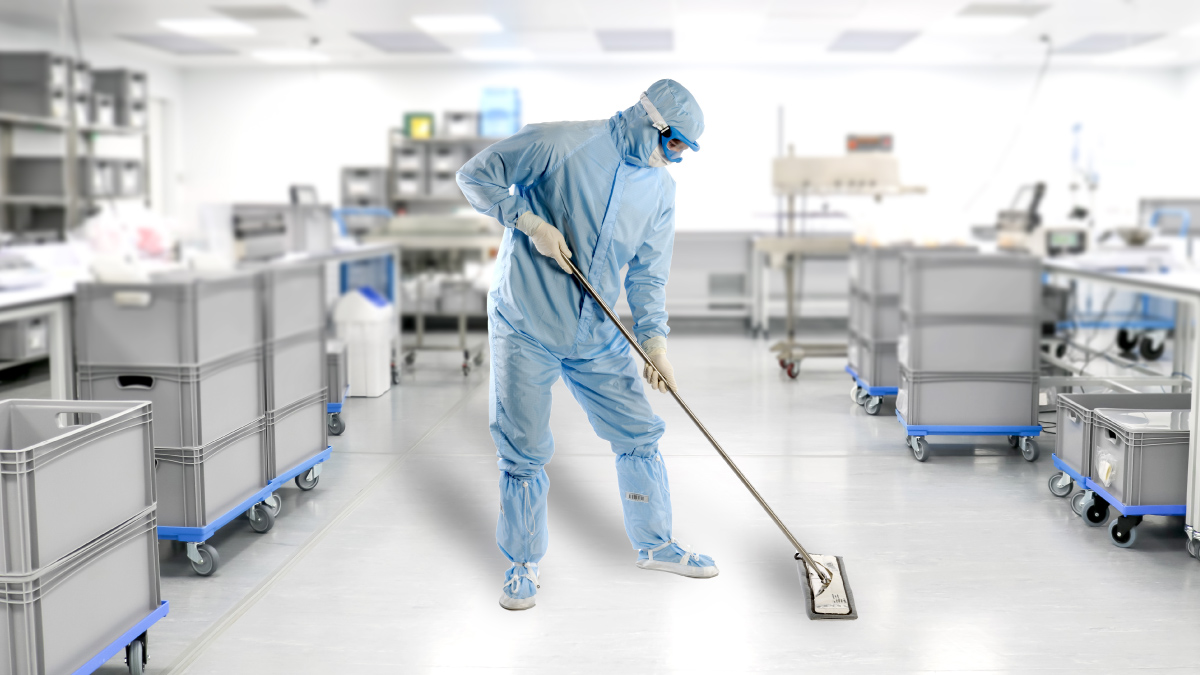
Cleanrooms vary in size from small units, perhaps containing one isolator, to very large microchip manufacturing plants. The same cleaning principles will apply whatever the size of the manufacturing operation but the scale of cleaning will be very different.
The size and type of cleaning equipment needed, purchase and storage of cleaning materials and staff requirements will all increase with larger and more complex cleanroom facilities. For a large operation the cleaning programme will be a significant cost and is likely to be managed by a dedicated team. In a small cleanroom the cleaning programme may be managed and carried out by the area production staff as part of their normal duties.
Operational hours
All staff involved in cleanroom operations have a responsibility for a “clean-as-you-go” approach. This ensures that staff are aware of the cleaning requirements and help to maintain the facility in good condition throughout production.
In addition it is preferable for the full, regular cleaning cycle to be carried out when the cleanroom is not producing product. This gives better access for the cleaning staff and their equipment without disruption to production activities. When wet cleaning is being performed surfaces may become slippery and this can pose a slip hazard especially on smooth flooring surfaces.
During cleaning operations the actions of the cleaning staff may generate temporary increases in airborne particulate which could be damaging to product being manufactured at the same time.
For these reasons it is preferable to time the cleaning programme around the operational hours.
When the production operation is continuous and cleaning must be carried out during production it is especially important to ensure that any cleaning operations are safe and do not compromise the process.
Production equipment and machinery
The presence of production machinery and equipment in the controlled area will present two issues. The equipment itself may disperse particulate or vapour into the area and so contribute contamination during operations. Removal of the contaminants produced by equipment may require specific cleaning methods and cleaning agents.
Machinery and equipment may also require cleaning both externally and internally on a regular basis and this needs to be included in the cleaning programme. Any cleaning procedures for machinery must enable the required cleaning to take place without risk to the equipment or cleaning staff. When cleaning of this type is performed a Health and Safety risk assessment is likely to be required and appropriate safety procedures must be in place and strictly followed.
Cleaning of machinery may also produce significant additional contamination of adjacent areas and this must be considered when developing the overall cleaning plan.
Staff numbers
Cleanroom staff will create particulate contamination in their area of work; more particulate will be produced with increased activity. The numbers of staff and their activity level must therefore be taken into account when assessing cleaning requirements. Contamination from discarded cleanroom disposables and clothing together with the associated packaging will also increase. It is likely therefore that as the number of operational staff increases so too will the requirement for cleaning and housekeeping.
Types of contaminant present
Particulate from cleanroom staff will be viable and non-viable particulate from lost skin fragments together with particles and fibres from clothing. These particulates will be mostly microscopic and removed by standard cleanroom cleaning techniques.
Some manufacturing operations however may produce contamination which presents a chemical, microbiological or radiation hazard. This may occur for example when cytotoxic drugs are being prepared or during virus production for vaccine manufacture. Cleaning protocols for these contaminants need to be established and all staff made aware of the procedures for cleaning and disposal of contaminated materials. Contamination may also occur which is difficult to remove. This contamination may be present in particular work stations or departments where materials such as adhesives, sealants and inks are used as part of the manufacturing process.
These types of materials will not be removed by normal cleanroom cleaning methods or products and will require special procedures to ensure they are effectively removed and that no residues remain.
Health and safety requirements
Cleaning operations will take place in enclosed cleanrooms, usually not during normal production hours and with minimum staff present.
The cleaning procedures may include the use and dilutions of different chemicals some of which may be harmful or flammable.
Cleaning staff may have to access difficult areas and work on or near electrically powered machinery. Application of solutions to smooth surfaces such as floors can generate a slip hazard. Hazardous materials may be present in the controlled areas both as contaminants and as process components. Cleaning staff may need to be equipped with items of personal protective equipment (PPE) which must be compatible with the cleanroom environment.
The full extent of the cleanroom cleaning requirements and associated hazards should be established when developing a cleaning system and a health and safety risk assessment carried out on all aspects of the cleaning programme to address these types of issues.
Staff Availability
All cleanroom staff have responsibilities for keeping the area clean. As a minimum this involves the correct disposal of packaging, consumable items and re-usable clothing and removal of visible contamination. A “clean-as-you-go” philosophy is usually adopted with each member of staff responsible for the general care and cleanliness of their work area and may include regular wipe down of critical surfaces.
However most cleanroom cleaning is carried out separately from production activities and undertaken by trained cleaning staff.
Staff performing these duties must be thoroughly trained in cleaning operations and also in the general rules for staff operating in the cleanroom.
Cleaning staff have a great influence on the continued successful operation of the facility and may often work unsupervised. Training should therefore include basic cleanroom technology and the requirements for GMP.
Cleaning staff must be equipped with full cleanroom clothing as well as any PPE and follow the changing procedures for each area.
When large areas require cleaning, or for special cleandowns e.g. following a new build, specialised cleanroom-cleaning contractors can provide a good alternative to in-house staff.
Cost
Once the cleaning requirement has been established it is advisable to investigate various options to obtain the best solution at the lowest cost. The total cost of a cleanroom cleaning programme is made up of a range of items including staff, cleaning materials, wastage and disposal charges.
It is often necessary to assess different cleaning materials both for their cleaning efficiency and ease of use in a specific location. For example in a cleanroom with a large surface area and low cleanliness classification it may be satisfactory to mop the floor using a mop and a two or three bucket system using concentrated cleaning agents or disinfectants diluted by staff at point of use. For cleanrooms with smaller floor area and for those with high classifications, sterile mops, pre-impregnated with a volume of RFU (ready for use) chemical, may be more cost effective.
Cleaning equipment can be purchased or leased and some items such as mops and wipes may be re-usable and require a cleaning and decontamination service. It is beneficial to discuss the full cleaning programme with specialist suppliers of cleanroom products who will be able to provide advice and information on suitable products and the most cost effective solutions.