Big Blue Blog - Cleaning Plans, SOPs and Records
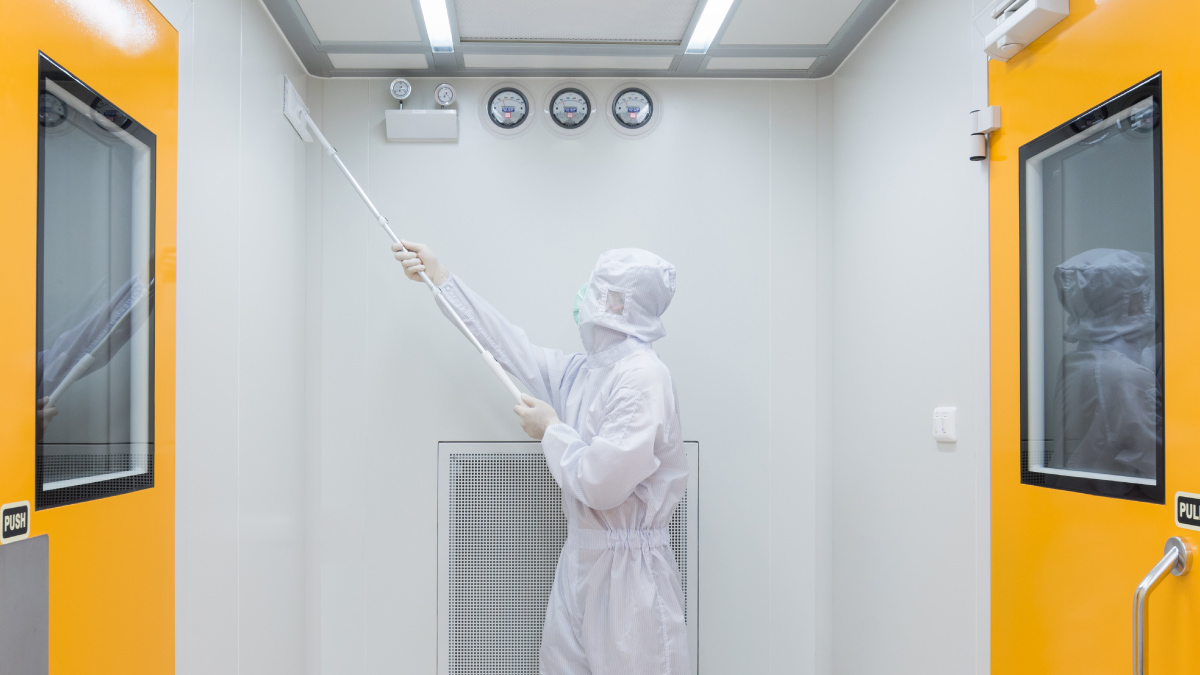
Once all information relevant to the cleanroom cleaning requirements has been assessed a cleaning plan should be created.
The plan will provide clear information when discussing requirements with cleaning suppliers, and for developing cleaning standard operating procedures (SOPs) and a staff training programme.
Any changes to the cleanroom facility or its function must be assessed using the cleaning plan and a new revision of the plan produced when required with traceability of the changes implemented. A cleaning plan will be a useful reference when cleaning validations and re-qualifications are performed and is also essential for customer or compliance audits.
The cleaning plan will define;
- What is to be cleaned
- How the cleaning will be carried out
- When the cleaning is to be carried out
- Who is responsible for cleaning
When producing a cleaning plan the different cleanliness zones and areas of greatest risk to product should be detailed.
Locations of manufacturing equipment, dedicated cleaning equipment e.g. connection points for built-in vacuum system and garment issue and disposal points should be shown.
Any areas of notable hazards, first aid boxes and emergency exits must be clearly identified.
The cleaning plan will include details of the cleaning equipment and chemicals and the associated dilution and application rates specific to the production unit.
The order, frequency and methods of cleaning will also be chosen to suit each unit however the following principles of cleanroom cleaning will apply to all plans.
- Cleaning must start with the cleanest area and finish with the least clean area.
- Cleaning follows the air pressure cascade in a series of cleanrooms from the highest pressure to the lowest pressure.
- In a cleanroom cleaning starts at the point furthest from the exit and works towards the exit.
- Cleaning is carried out in a series of steps starting with the removal of visible contamination followed by the removal of microscopic particulate.
- When a chemical sanitiser is used the correct concentration, volume and surface contact time must be clearly stated.
- No cleaning equipment or products must be specified which will produce particulate contamination or leave harmful residues.
- Cleaning operations which have the potential to cause contamination e.g. emptying garment discard bins, must be identified and confined to non-critical areas.
- Any staff involved with cleaning must be properly trained and equipped.
- Any cleaning operations involving hazardous materials must be identified and all aspects of cleaning and disposal clearly described.
- All cleaning activities need to be appropriately recorded. The cleaning records need to be reviewed on a scheduled frequency and retained for future reference.
For a small operation a cleaning plan may provide sufficient cleaning information. It is usually beneficial however to produce standard operating procedures (SOPs) for each cleaning task. SOPs not only provide detailed instructions for anyone performing a cleaning task but also form the basis for staff training.
Cleaning logs are completed by staff to ensure that all cleaning operations are being carried out correctly and on-time. These documents act as a check list for the cleaning staff and can also provide evidence that the cleaning procedures are being followed correctly.
Fig 1. A series of diagrams of the cleanroom areas to be cleaned is a clear way to develop a cleaning rationale.