Class 6 Cleanroom Louth
In Louth – Lincolnshire, Micronclean operates one of the most technically advanced ISO Class 6 (GMP Grade C) Cleanroom Laundries in Europe, with the capacity to process more than 120,000 items a week.
The Louth plant is highly automated and was purpose-built to exploit the power within our Protrack garment tracking system. When garments arrive at our site they are scanned individually with the transponder, logging the garment onto the site and opening its processing record, then entering it onto a delivery schedule.
Garments are then transferred into an overhead storage bag in order to weight them for correct loading. The machine received a ready to load signal and the soiled garments are dropped into the industrial washing machine, ready to be processed. The washing machine process is then started and controls the appropriate level of detergents, water and heat.
Barrier washing machines are used to transfer garments into the ISO Class 6 cleanroom, and placed in clean work storage containers until they are ready for the ‘finishing’ stage.
Garments are once again scanned using the transponders and put onto a specialist hanger attached to a automatic rail system. This rail system then conveys the garment to a ‘Tunnel Finisher’ dryer.
Once dried the garments are passed through quality inspection stations where they are assessed. Any items identified as non-confirming are logged and sent to the relevant area for rework.
Items that are fit for purpose are sent to automatic folding machines followed by automatic wrapping machines. Completed items are then sent via flatbed conveyers to a transponder reading device. Garments are fixed into a specially designed hanger, which conveys the garment into a large store facility. Items are designated to a specific storage lane according to the scheduled delivery route which is followed by an automatic sortation using a series of computer controlled rails. This enables garments to be placed into delivery areas and sorted into lot numbers prior to being packed into clean work hampers.
The consignment is then packed into the delivery vehicle ready for despatch back to our customer's site.
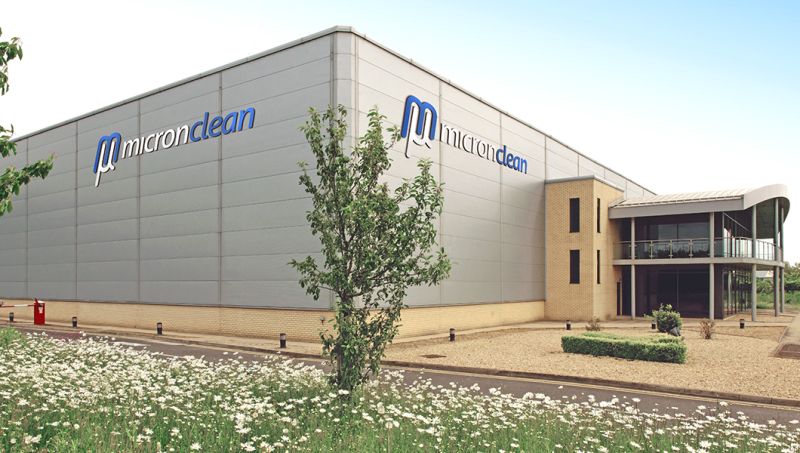