Big Blue Blog - Mops
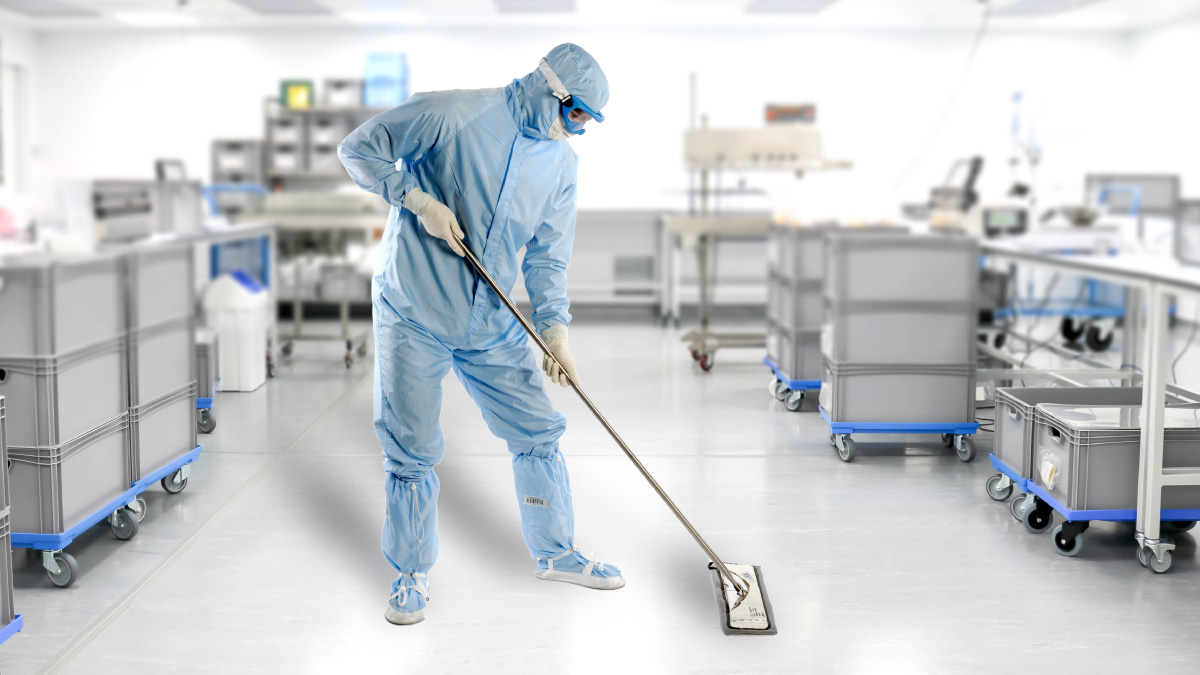
Cleanroom mops clean effectively by wiping surfaces and so can be employed to remove the invisible contamination which cannot be removed by vacuum cleaning. Mops are particularly suitable for large flat areas such as floors and walls and different designs of mop head, frame and handle are available for different cleaning operations and locations. Mops can also be used to quickly apply anti-microbial chemicals to large surfaces.
Mops should be used in long overlapping strokes so that all the surface area is covered sequentially.
The cleaning action of mopping comes from the physical drag forces applied to the particulate and removal efficiency is greatly enhanced when a wet mopping system is used. The greater the surface area of the mop in contact with the surface the better the wiping action and so any cleanroom mop should provide intimate surface contact. Mops manufactured from microfibre are especially efficient for this reason.
All materials used in the construction of the mop, the mop frame and the handle should not be a source of fibre or particulate which could contaminate the cleanroom.
All components should be easily cleaned, decontaminated and sterilised if necessary. The mop must also be able to withstand the abrasion from surface contact, which can be especially severe with some non-slip cleanroom flooring finishes. Disposable cleanroom mops are available but due to the high cost of disposable products re-usable mop systems are normally employed.
There are two main systems available for re-usable cleanroom mopping.
- Impregnation and rinse bucket-system
- Pre-impregnated system
Bucket system
This is the traditional mopping system modified for cleanroom use.
A bucket is used to impregnate the mop with cleaning agent and then to rinse the mop between applications.
This single bucket system has the obvious disadvantage that from the first rinse onwards the cleaning solution becomes increasingly contaminated until it is merely re-contaminating the surface with each mopping. It is also possible that harmful contamination from a local area will be removed and then spread throughout a much greater area.
To introduce a rinse stage a two or three bucket system can be used which will also usually include a ringer to remove excess liquid from the mop. The whole system is usually mounted on a large, wheeled trolley.
For a two bucket system, bucket one is filled with the cleaning solution and the other with rinse water. The mop is impregnated with cleaning solution, wrung to remove excess liquid and applied to the floor. Once the operator decides that the mop requires rinsing it is placed in the rinse water bucket, wrung again and then re-impregnated in the cleaning solution and the cycle repeated. There will be carry-over from the rinse water which gradually dilutes the cleaning agent and the rinse water becomes contaminated thus reducing its ability to clean the mop between each use.
The three bucket system adds a discard bucket. Following impregnation and use as much as possible of the contaminated liquid is removed into the discard bucket by wringing.
The mop can then be rinsed, wrung and re-impregnated with new cleaning chemical as in the two bucket system. The three bucket system has the same dilution and carry-over problems as the two bucket system but they are greatly reduced by the addition of the third bucket.
Once the cleaning operation has been completed, or the cleaning agent needs replacing, the buckets must be emptied and cleaned before being stored dry. It is preferable to wipe down the equipment after use to ensure that no liquid remains which can quickly become a source of microbiological contamination.
Bucket systems are widely used for low grade areas and for cleanrooms with large floor areas and easy access. The equipment trolley is large and the buckets must be filled and emptied so adequate provision must be made for chemical and equipment storage and waste liquid disposal. It is advisable to carry out a Health and Safety risk assessment, which includes manual handling, on cleaning operations using bucket mopping systems.
Pre-impregnated system
This modern simplified mopping system was developed specifically for cleanroom cleaning and does not require buckets or wringer. In this mopping system the mop head is contained within a sealed pouch. The pouch is opened just before use and a small volume (approx. 200mls) of pre-diluted cleaning chemical added.
The mop is allowed to absorb the entire added chemical before being removed and fitted to the frame and handle. A specific square meterage of surface (usually around 20m2) is then mopped. Once this area has been covered the mop is removed from the frame and discarded for cleaning, decontamination and re-pouching. A new mop is then used in the same way for subsequent areas.
Mops may be sourced which are packed singly or in multiples allowing several to be impregnated at one time. It is also possible to obtain mops which are already impregnated with the chosen chemical and in this case the mop only requires removal from the pouch and is then ready for use. Sterile mops are available if needed. As the mops are pre-impregnated with the correct volume of chemical to cover a specific area all the chemical is used for cleaning or disinfection and so no wasted excess chemical remains to be discarded at the end of the cleaning procedure.
This system removes the risks of cross contamination and chemical dilution present with bucket systems and the only equipment required is the mop frame, handle, mop heads, discard bag and pre-measured doses of the correct chemical. If the mop heads are supplied pre-impregnated with chemical then this further reduces the equipment needed.
As there is no handling of large volumes of chemicals the Health and Safety hazards associated with chemical dilution and the lifting of large buckets are also greatly reduced. This cleanroom mopping technique is especially suited to high grade cleanrooms and for those with restricted access.